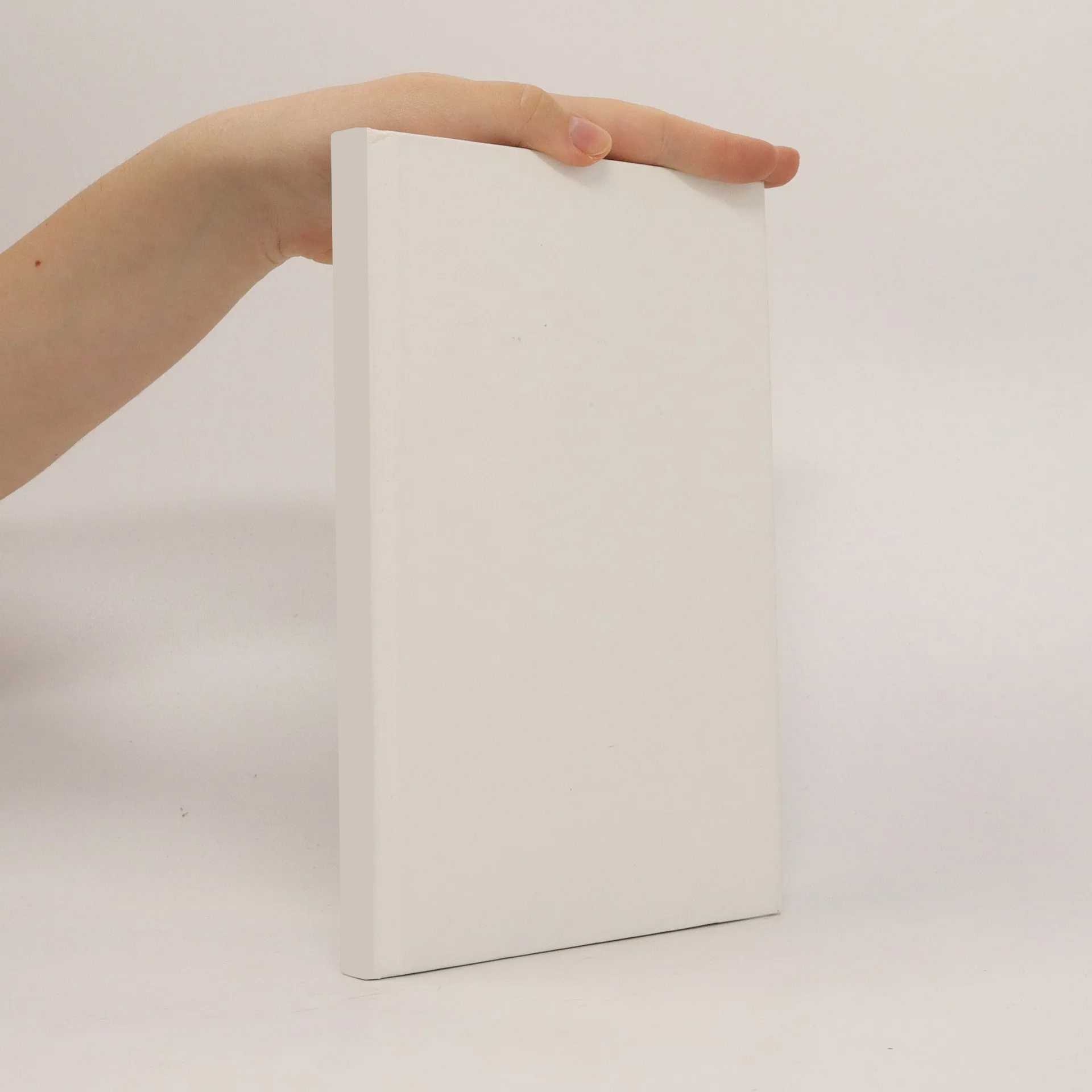
Thermal and electromagnetic modeling of a canned switched reluctance machine
Authors
Parameters
More about the book
This thesis presents an accurate electromagnetic and thermal analysis of a canned switched reluctance machine (SRM) as a pump driver. The first chapter introduces the applications of canned SRMs in pumping industry. The structure and material of cans are discussed in detail. The second chapter studies the design principles, including the geometry, windings and control. Also, the dynamic simulation by FEM in 3 dimensions is carried out. In the third chapter, a novel thermal network is introduced characterized by a compensation element. The model is simple and fast while high accuracy is achieved by comparing with FEM. The can loss is the most obvious source and is analyzed in the fourth chapter. Also, the iron loss is analyzed using flux density waveform. Both hysteresis and eddy current losses are calculated separately. In the fifth chapter, the MMF distribution is modeled. Different models are discussed. The first model aims to investigate how each turn is fixed onto a tooth while the second is simplified by transferring a coil onto the stator slot. In the sixth chapter, an analytical magnetic network is created based on MEC method. All elements are adjustable according to the degree of saturation on different parts. The air gap reluctance is calculated using arcs and straights, which can be used in any other geometry without empirical estimations. The flux leakage in the slot and end part is also taken. In the seventh chapter, the can loss is reduced. Strategies come from the rate of change of phase current, making slot cavities, axial separation of the machine body, using longer cans and arrangement of turns in a coil. All of these makes detailed design of SRMs especially when cans are used.
Book purchase
Thermal and electromagnetic modeling of a canned switched reluctance machine, Qiang Yu
- Language
- Released
- 2012
Payment methods
- Title
- Thermal and electromagnetic modeling of a canned switched reluctance machine
- Language
- English
- Authors
- Qiang Yu
- Publisher
- Shaker
- Released
- 2012
- ISBN10
- 3844015094
- ISBN13
- 9783844015096
- Series
- Forschungsberichte Elektrische Antriebstechnik und Aktorik
- Category
- University and college textbooks
- Description
- This thesis presents an accurate electromagnetic and thermal analysis of a canned switched reluctance machine (SRM) as a pump driver. The first chapter introduces the applications of canned SRMs in pumping industry. The structure and material of cans are discussed in detail. The second chapter studies the design principles, including the geometry, windings and control. Also, the dynamic simulation by FEM in 3 dimensions is carried out. In the third chapter, a novel thermal network is introduced characterized by a compensation element. The model is simple and fast while high accuracy is achieved by comparing with FEM. The can loss is the most obvious source and is analyzed in the fourth chapter. Also, the iron loss is analyzed using flux density waveform. Both hysteresis and eddy current losses are calculated separately. In the fifth chapter, the MMF distribution is modeled. Different models are discussed. The first model aims to investigate how each turn is fixed onto a tooth while the second is simplified by transferring a coil onto the stator slot. In the sixth chapter, an analytical magnetic network is created based on MEC method. All elements are adjustable according to the degree of saturation on different parts. The air gap reluctance is calculated using arcs and straights, which can be used in any other geometry without empirical estimations. The flux leakage in the slot and end part is also taken. In the seventh chapter, the can loss is reduced. Strategies come from the rate of change of phase current, making slot cavities, axial separation of the machine body, using longer cans and arrangement of turns in a coil. All of these makes detailed design of SRMs especially when cans are used.