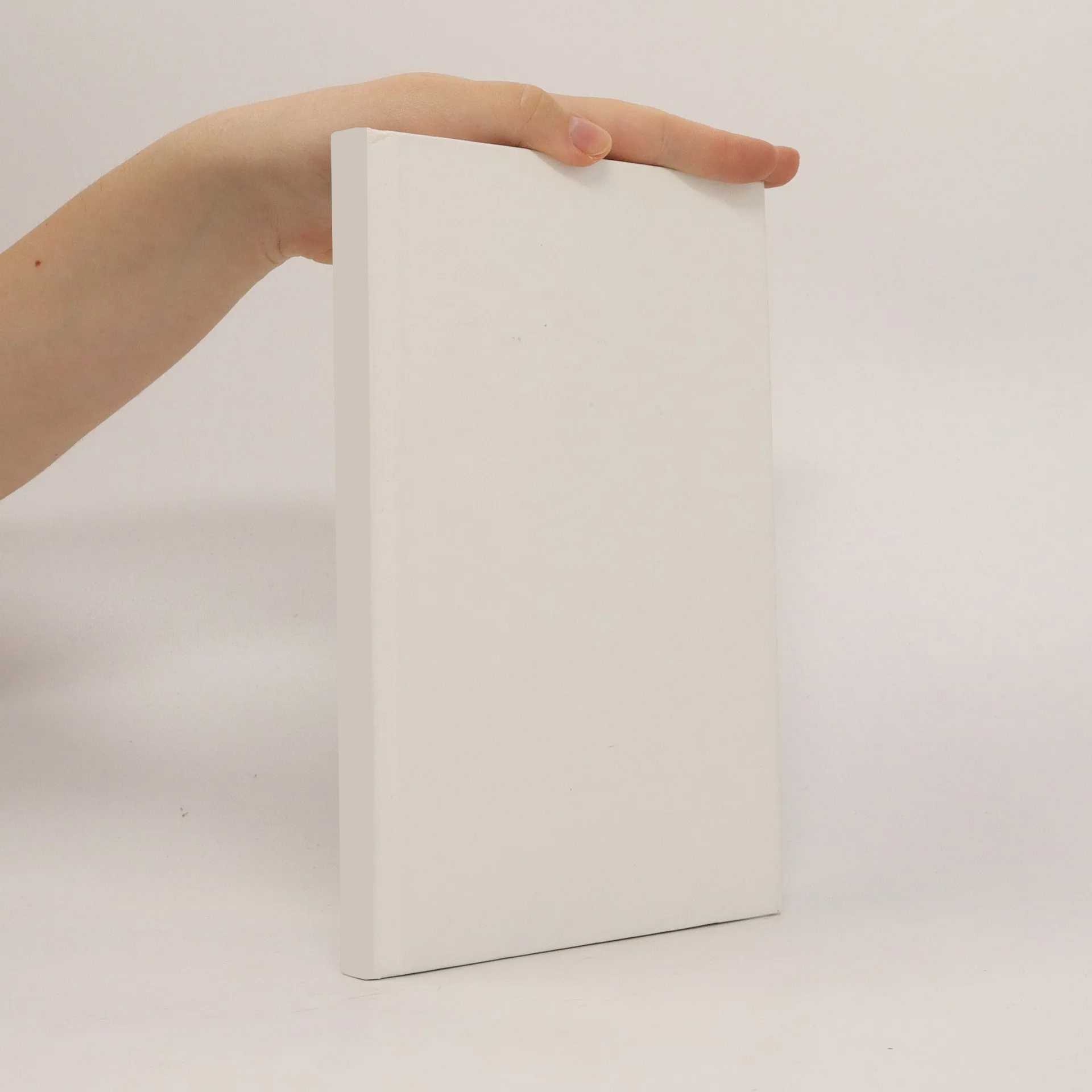
Quantification of fluid-structure interaction effects during water hammer in piping systems
Authors
Parameters
More about the book
Fast transient events such as water hammer are potentially dangerous for any piping system. In some cases, an accurate calculation must include fluid-structure interaction (fsi). The important question is: when is fsi important and has it to be taken into account? Therefore, fsi effects in an industry-oriented piping system have been investigated and quantified. Two-way junction coupling effects were resolved only in the short system with the medium and long bends, where the differences originated from the bend geometry. The coupling is independent of the excitation. Coupled simulations showed that basically the strength of the coupling is a function of the amount of fluid mass contained in the vertical pipe section between the parallel levers. Using the simulation data and the analogy with the two-mass oscillator, it is possible to predict the strength of the coupling on the basis of the geometry and the mass of the bend. Unsteady friction was analysed in oscillating pipe flow and water hammer flow. The good agreement between the wall shear stresses of the analytical solution, CFD simulations and the measurements verified the numerical model and the measurement method. In the case of water hammer flow, differences between the wall shear stress distributions of the CFD simulations and the measurements originated from the limited frequency resolution of the hot film probe. Finally, the results of a CFD simulation of water hammer were compared with the results of 1D calculations using a quasi-steady friction model and unsteady friction models. No model was able to reproduce the fluid damping occurring in the CFD simulation because it originated from dissipation close to the wall and not in loss of momentum caused by friction at the wall.
Book purchase
Quantification of fluid-structure interaction effects during water hammer in piping systems, Stefan Riedelmeier
- Language
- Released
- 2017
Payment methods
- Title
- Quantification of fluid-structure interaction effects during water hammer in piping systems
- Language
- English
- Authors
- Stefan Riedelmeier
- Publisher
- Shaker Verlag
- Released
- 2017
- ISBN10
- 3844050353
- ISBN13
- 9783844050356
- Series
- Schriftenreihe des Lehrstuhls für Prozessmaschinen und Anlagentechnik
- Category
- University and college textbooks
- Description
- Fast transient events such as water hammer are potentially dangerous for any piping system. In some cases, an accurate calculation must include fluid-structure interaction (fsi). The important question is: when is fsi important and has it to be taken into account? Therefore, fsi effects in an industry-oriented piping system have been investigated and quantified. Two-way junction coupling effects were resolved only in the short system with the medium and long bends, where the differences originated from the bend geometry. The coupling is independent of the excitation. Coupled simulations showed that basically the strength of the coupling is a function of the amount of fluid mass contained in the vertical pipe section between the parallel levers. Using the simulation data and the analogy with the two-mass oscillator, it is possible to predict the strength of the coupling on the basis of the geometry and the mass of the bend. Unsteady friction was analysed in oscillating pipe flow and water hammer flow. The good agreement between the wall shear stresses of the analytical solution, CFD simulations and the measurements verified the numerical model and the measurement method. In the case of water hammer flow, differences between the wall shear stress distributions of the CFD simulations and the measurements originated from the limited frequency resolution of the hot film probe. Finally, the results of a CFD simulation of water hammer were compared with the results of 1D calculations using a quasi-steady friction model and unsteady friction models. No model was able to reproduce the fluid damping occurring in the CFD simulation because it originated from dissipation close to the wall and not in loss of momentum caused by friction at the wall.