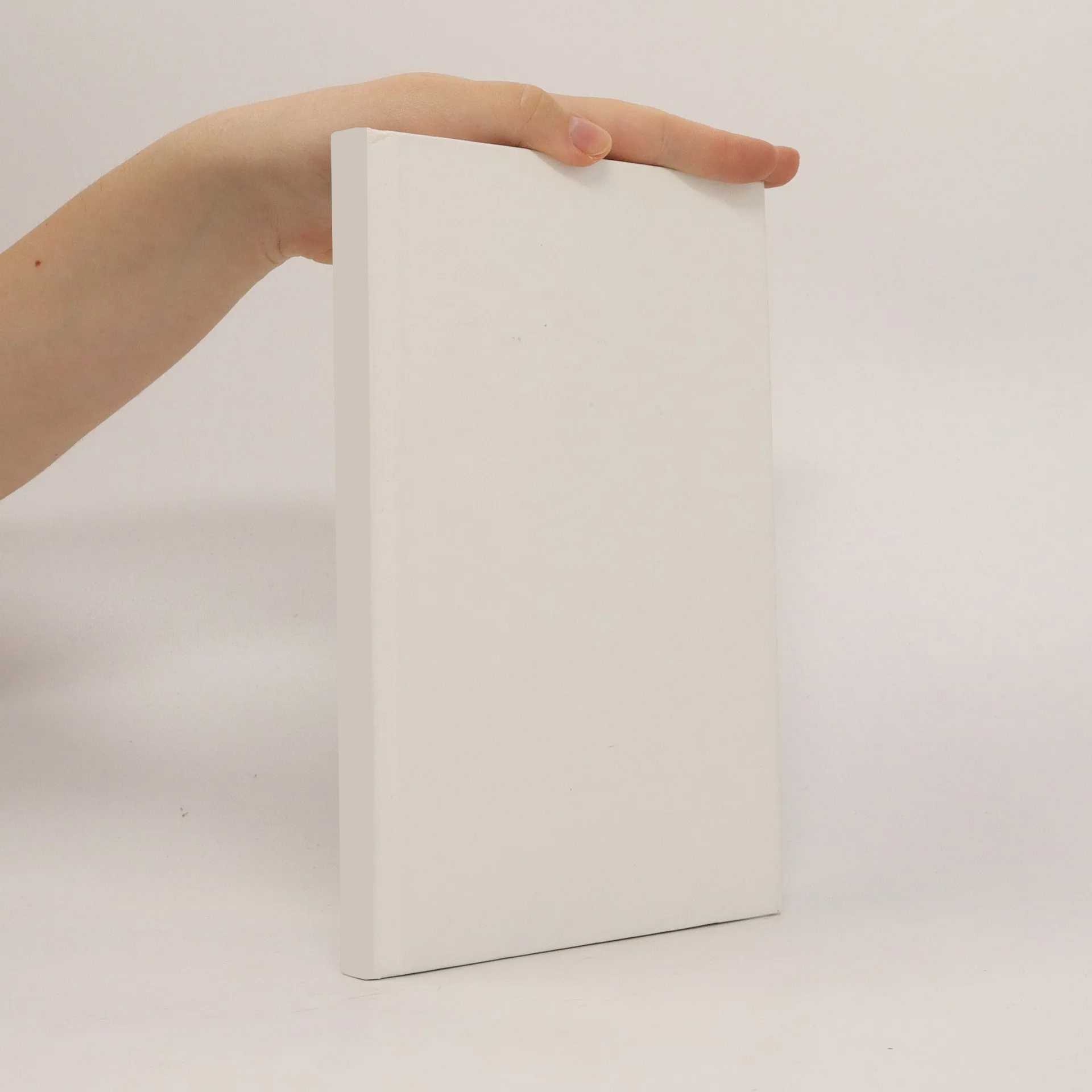
Multidisciplinary gradient-based optimization of radial turbines
Authors
Parameters
More about the book
This thesis deals with the design and improvement of a turbocharger's radial turbine. For this purpose, a custom automated optimization work flow is devised and applied to a radial turbine. The method is multidisciplinary, i. e. a range of cost functions are implemented and used as either objectives or constraints: The polar moment of inertia, the wheel's mass and center of gravity, stresses, the blade's eigenfrequencies, its response to a forced excitation, the turbine's efficiency and the delivered torque. The applied optimization work flow uses gradient information to propose new design iterations. Using gradients in addition to plain function evaluations promises a drastic speed-up in the optimization process, in particular when high-dimensional design spaces are studied. The applied gradient calculation process involves determining surface sensitivities, which yield valuable insights for radial turbine designers as they display how geometrical changes affect the relevant cost functions. Among the studied objectives and constraints, the forced response stands out as it marks a small novelty in the field of gradient-based radial turbine optimization: The wheel's response to a harmonic forced excitation utilizing an aeroacoustically motivated damping is studied. The applied method imposes little computational cost as a coupling to fluid simulations is avoided. A number of optimization studies are conducted successfully to illustrate the potential of the gradient-based optimization work flow. The applied optimization work flows are capable of handling complex design problems, prove cost effective and reveal interesting insights into radial turbine design. The method is of industrial interest, which is underscored by the inclusion of commercial software.
Book purchase
Multidisciplinary gradient-based optimization of radial turbines, Nicolas Lachenmaier
- Language
- Released
- 2023
Payment methods
- Title
- Multidisciplinary gradient-based optimization of radial turbines
- Language
- English
- Authors
- Nicolas Lachenmaier
- Publisher
- Shaker Verlag
- Released
- 2023
- ISBN10
- 3844089349
- ISBN13
- 9783844089349
- Series
- Forschungsberichte aus dem Institut für Gasturbinen, Luft- und Raumfahrtantriebe
- Category
- University and college textbooks
- Description
- This thesis deals with the design and improvement of a turbocharger's radial turbine. For this purpose, a custom automated optimization work flow is devised and applied to a radial turbine. The method is multidisciplinary, i. e. a range of cost functions are implemented and used as either objectives or constraints: The polar moment of inertia, the wheel's mass and center of gravity, stresses, the blade's eigenfrequencies, its response to a forced excitation, the turbine's efficiency and the delivered torque. The applied optimization work flow uses gradient information to propose new design iterations. Using gradients in addition to plain function evaluations promises a drastic speed-up in the optimization process, in particular when high-dimensional design spaces are studied. The applied gradient calculation process involves determining surface sensitivities, which yield valuable insights for radial turbine designers as they display how geometrical changes affect the relevant cost functions. Among the studied objectives and constraints, the forced response stands out as it marks a small novelty in the field of gradient-based radial turbine optimization: The wheel's response to a harmonic forced excitation utilizing an aeroacoustically motivated damping is studied. The applied method imposes little computational cost as a coupling to fluid simulations is avoided. A number of optimization studies are conducted successfully to illustrate the potential of the gradient-based optimization work flow. The applied optimization work flows are capable of handling complex design problems, prove cost effective and reveal interesting insights into radial turbine design. The method is of industrial interest, which is underscored by the inclusion of commercial software.