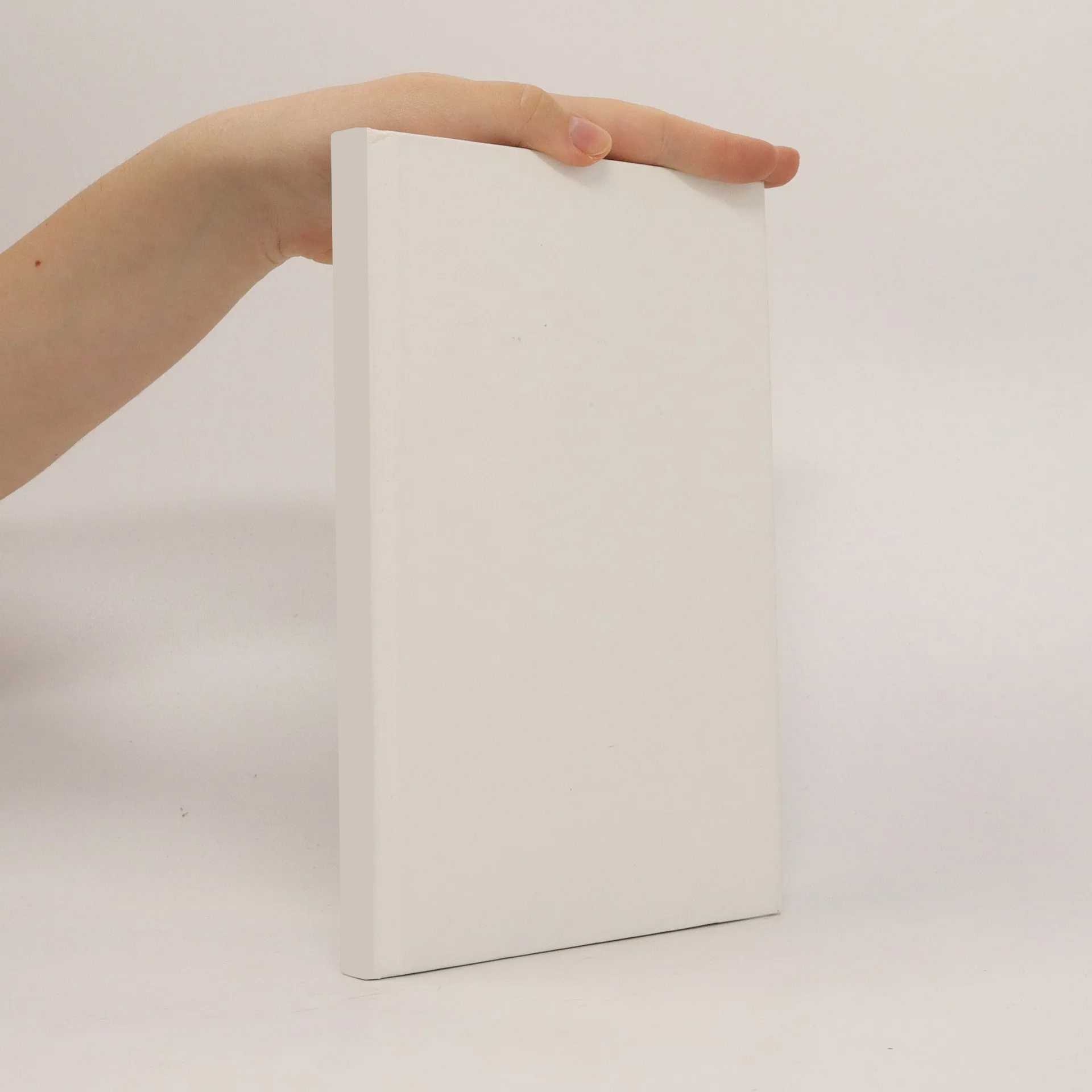
More about the book
In this work, the thermal, metallurgical, and the mechanical fields of DC casting are modeled. The attention is focused on the mushy state of alloy where the chances are high for the hot tearing. The heat conduction and metallurgical phase-change phenomenon are modeled together in a strongly coupled manner. The influence of casting speed, secondary cooling, and melt superheat on the sump parameter and stress-strain evolution are studied thoroughly. It is proved that through the ramping procedure, the vulnerability of start-up phase can be lowered. Ramping delays the time and increases the billet height to reach the steady state. Increase in casting speed, secondary cooling, and melt temperature promote the chances of hot tearing. The influence of secondary cooling parameters are studied in depth. Increased cooling reduces stresses in the mushy at the steady state and rises probability of hot tearing during the startup phase whereas the reduced cooling influences in exactly opposite manner. Therefore, an attempt is made to illustrate the importance of varying the secondary cooling with respect to time. It is demonstrated that through the optimized secondary cooling, the evolution of residual stresses and inelastic strains can be lowered.
Book purchase
Thermomechanical simulation of direct chill casting, Ashok Kumar Nallathambi
- Language
- Released
- 2010
Payment methods
No one has rated yet.