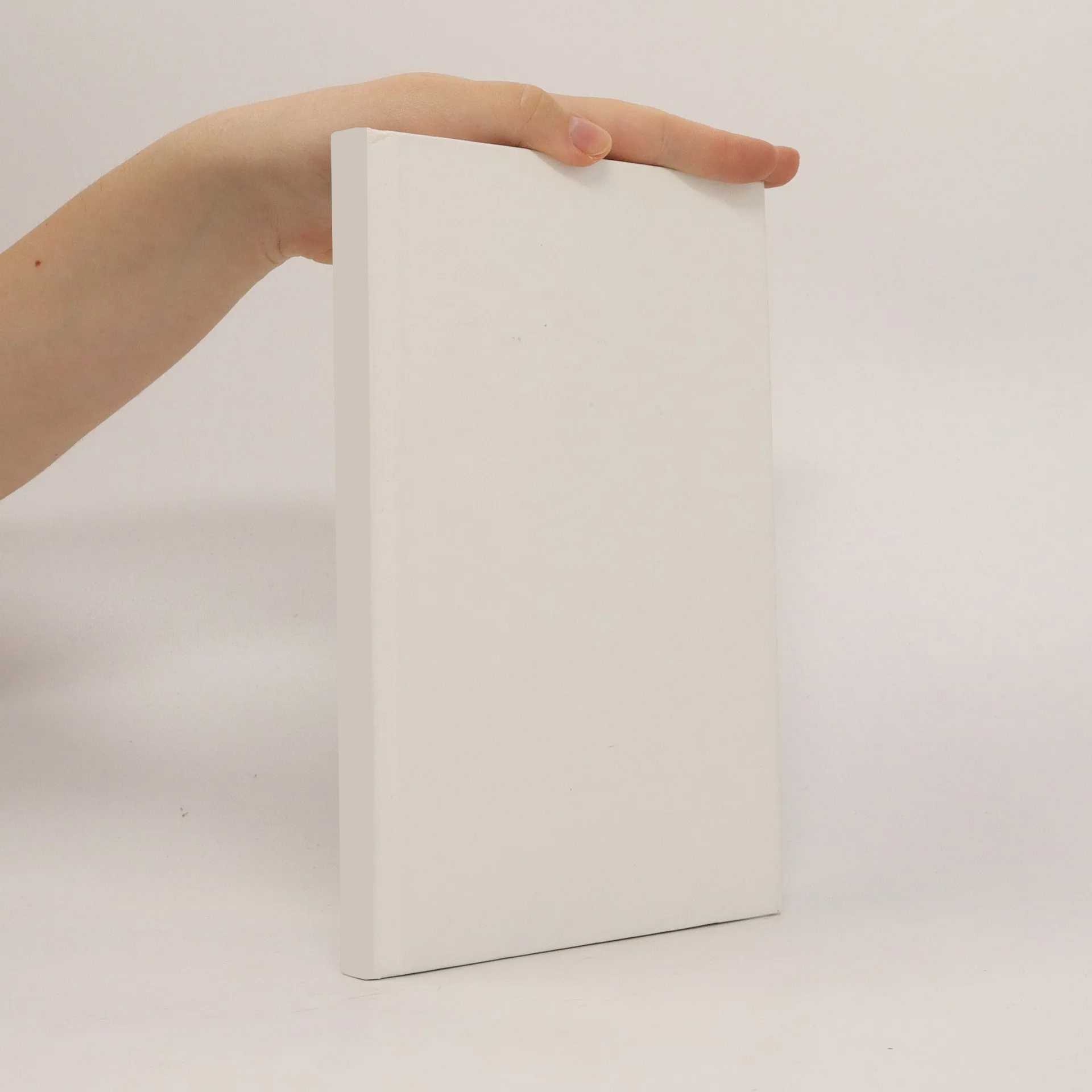
Model-based reduction of energy consumption of the weft insertion process in air-jet weaving technology
Authors
Parameters
More about the book
The goal of this work is the development of an optimised profiled reed for the reduction of energy consumption of air-jet weaving machines. First, a theoretical model of the air flow in the tunnel and a boundary layer study around the weft yarn are proposed and analysed. An optimisation study is conducted on the standard reed tunnel geometry. The optimisation leads to the design of five new tunnel geometries. The air flow inside the reed tunnels is investigated by means of CFD simulation. A final concept of optimised reed is then chosen, manufactured and tested. During the tests at ITA it is quantified that 80 % of the mass flow rate, blown by the nozzle into the benchmark reed, dissipates through the reed dents. The tests confirm the simulation and show that, the volume flow rate required to drive the yarn inside the standard reed tunnel at 5 bar operating pressure can be achieved by employing the optimised reed at a lower pressure of about 3.5 bar. During the tests in the weaving mill, a constant production rate and a constant fabric quality are achieved at a lower working pressure by employing the optimised reed. The pressure reduction results into a decrease of the normal volume flow rate consumed by the machine and consequently into 21 % of cost savings. The payback period for the purchase of the optimised reed depend on the worldwide location of the weaving mill and are in a range between 3 and 11 months.
Book purchase
Model-based reduction of energy consumption of the weft insertion process in air-jet weaving technology, Corrado Grassi
- Language
- Released
- 2018
Payment methods
- Title
- Model-based reduction of energy consumption of the weft insertion process in air-jet weaving technology
- Language
- English
- Authors
- Corrado Grassi
- Publisher
- Shaker Verlag
- Released
- 2018
- ISBN10
- 3844058648
- ISBN13
- 9783844058642
- Series
- Textiltechnik
- Category
- University and college textbooks
- Description
- The goal of this work is the development of an optimised profiled reed for the reduction of energy consumption of air-jet weaving machines. First, a theoretical model of the air flow in the tunnel and a boundary layer study around the weft yarn are proposed and analysed. An optimisation study is conducted on the standard reed tunnel geometry. The optimisation leads to the design of five new tunnel geometries. The air flow inside the reed tunnels is investigated by means of CFD simulation. A final concept of optimised reed is then chosen, manufactured and tested. During the tests at ITA it is quantified that 80 % of the mass flow rate, blown by the nozzle into the benchmark reed, dissipates through the reed dents. The tests confirm the simulation and show that, the volume flow rate required to drive the yarn inside the standard reed tunnel at 5 bar operating pressure can be achieved by employing the optimised reed at a lower pressure of about 3.5 bar. During the tests in the weaving mill, a constant production rate and a constant fabric quality are achieved at a lower working pressure by employing the optimised reed. The pressure reduction results into a decrease of the normal volume flow rate consumed by the machine and consequently into 21 % of cost savings. The payback period for the purchase of the optimised reed depend on the worldwide location of the weaving mill and are in a range between 3 and 11 months.